Micromolding: Pushing the Boundaries of Miniaturization
Micromolding is yielding miniaturized, intricate parts that are enabling ground-breaking innovation and improved performance.
September 5, 2023
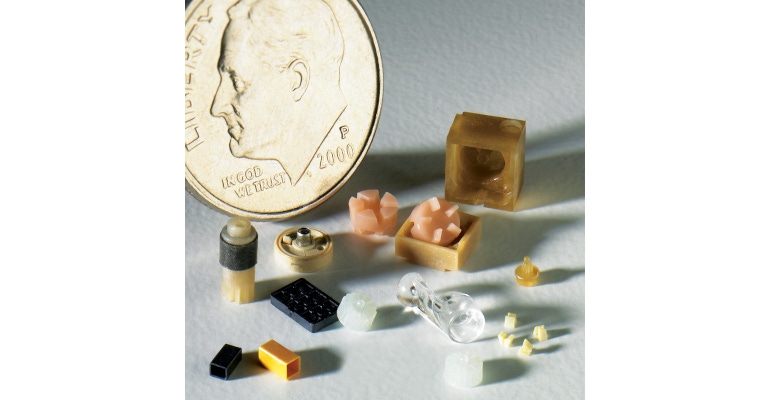
Miniaturization continues to advance medical treatments, consumer electronics, appliances, autos, and much more. Micromolding is helping bring about some of these advances.
“Micromolding is revolutionizing various market sectors by enabling the production of intricate and miniaturized components with exceptional precision and efficiency,” Paul Runyan, VP of Sales, Accumold, told Design News, MD+DI's sister publication. “Industries such as medical devices are at the forefront of benefiting from micromolding innovation. The medical sector relies on micro-molded components for applications like minimally invasive surgical instruments, drug-delivery systems, and implantable devices. The ability to manufacture complex geometries at micro-scale dimensions ensures enhanced patient outcomes, reduced invasiveness, and improved device performance. Additionally, the electronics sector is capitalizing on micromolding for compact and lightweight components used in wearables, sensors, and consumer electronics.
“As devices become smaller and more sophisticated, micromolding facilitates the production of intricate parts that maintain functionality and reliability while meeting the demands of the modern tech-savvy consumer,” he adds.
Accumold will highlight micromolding’s potential at the upcoming BIOMEDevice Boston and MD&M Minneapolis shows. To understand the state of the art in micromolding and what to expect next, Design News asked Runyan a few questions ahead of the shows.
What markets are benefiting from micromolding advances today?
Runyan: Micro Optics is our fastest growing business unit and plays an important role at the distal end of medical devices when going into the heart or through arteries to diagnose or look at a specific organ. Consumer electronics OEMs are also heavy users of micro optics for “smart devices” with sensors or driverless technology in the automotive sector.
The advantages of micro molding are particularly evident due to its impact on improving product performance, cost-effectiveness, and design flexibility. The ability to create precision parts in high volumes allows many industrial sectors to meet the demands of industry focused on sustainability and technological advancement. In essence, micro molding's application across diverse market sectors is driven by its capacity to produce miniaturized, intricate, and high-quality components that pave the way for ground-breaking innovations and improved performance in a wide range of products.
What are the latest trends in micromolding?
Runyan: The landscape of micromolding is evolving with several key trends that are shaping its trajectory in various industries. One prominent trend is the integration of advanced materials into the micromolding process. As industries demand higher performance and unique material properties, micromolding is adapting to accommodate materials like bioresorbable polymers for medical implants, high-temperature thermoplastics for aerospace applications, and conductive materials for electronic components. This trend not only expands the range of potential applications but also drives innovation in material science and processing techniques to ensure optimal performance at micro-scale dimensions.
Another significant trend in micromolding is the convergence of automation and Industry 4.0 technologies. Manufacturers like Accumold are increasingly adopting automation solutions such as robotic handling systems, vision inspection, and real-time monitoring to enhance production efficiency, consistency, and quality control. Furthermore, the integration of data-driven insights and IoT connectivity is enabling predictive maintenance, process optimization, and rapid adjustments to production parameters. This trend not only streamlines the micromolding process for the benefit of customers, but also paves the way for more agile and responsive manufacturing systems that can cater to the evolving demands of industries ranging from healthcare to electronics.
High-cavitation micro tooling and high-velocity production volumes continue to drive innovation within the micromolding niche since historically the industry was founded on achieving tight tolerance, micro in size, or micro featured parts through single-cavity precision tooling. Consumer electronics OEMs need micro components but have demands in the 10s or 100s of millions of units, and this has been a major change for traditional micromolders, which have had to change and innovate to increase tooling cavitation and production capacity over the past 10 years.
As micromolding continues to evolve, these trends are playing a pivotal role in shaping the capabilities and potential of this cutting-edge manufacturing technique.
What is design for micromolding (DfMM) and why is it important?
Runyan: Design for micromolding (DfMM) is a strategic approach that involves tailoring the design of components and products specifically for the micromolding manufacturing process. It emphasizes creating designs that optimize manufacturability, functionality, and performance while accounting for the unique constraints and capabilities of micromolding technology. DfMM aims to streamline the production process, enhance part quality, and ultimately maximize the benefits of micromolding in terms of efficiency, cost-effectiveness, and precision.
DfMM focuses on several critical considerations to ensure successful micromolding. These include intricate geometries that can be accurately reproduced at the micro scale, appropriate material selection that aligns with the molding process, and the mitigation of potential challenges such as material flow, cooling, and part ejection. Additionally, DfMM addresses the minimization of features like undercuts that can complicate demolding, as well as the optimization of parting line locations to avoid complex tooling. By incorporating these considerations early in the design phase, DfMM aims to reduce the likelihood of design iterations, decrease production lead times, and ultimately yield parts that meet or exceed quality and functionality requirements.
The importance of DfMM cannot be overstated. As micromolding is employed across industries such as medical devices, electronics, and automotive, designing with micromolding in mind ensures that components can be reliably manufactured to meet stringent specifications. Effective DfMM practices lead to cost savings by reducing production complexities, minimizing material waste, and accelerating time-to-market. Furthermore, DfMM facilitates the realization of innovative designs that exploit the unique capabilities of micro molding, enabling the creation of intricate and highly functional parts that might not be achievable through other manufacturing methods.
How should product design engineers work with micromolding experts?
Runyan: From the perspective of the subcontract micromolder, collaboration with product design engineers is paramount for optimizing outcomes in micromolding projects. Close communication from the early design stages allows the micromolder to provide valuable insights into the manufacturability of the proposed designs. By sharing expertise on micromolding constraints, material properties, and tooling considerations, the molder can guide design engineers towards creating components that align seamlessly with the capabilities of the micromolding process. This collaboration fosters the identification and resolution of potential challenges, such as complex geometries, undercuts, or ejection issues, before they become costly problems during production. Regular feedback exchanges and iterative design adjustments based on the molder's expertise contribute to the creation of designs that are not only functional and aesthetically pleasing but also practical for efficient micromolding production.
From the customer's perspective, the partnership with the subcontract micromolder is integral to achieving successful project outcomes. Design engineers should view the micro molder as a collaborative partner rather than a mere production entity. By involving the molder early in the design process, engineers can harness their specialized knowledge to optimize designs for the micromolding process. This collaboration ensures that design choices are informed by a deep understanding of material behavior, tooling limitations, and production nuances. Such proactive engagement enhances the likelihood of meeting project goals, maintaining budget constraints, and adhering to project timelines. Ultimately, the symbiotic relationship between the customer's design team and the micromolder fosters a dynamic exchange of expertise, resulting in innovative yet manufacturable designs that push the boundaries of micromolding technology.
Are there new material or machinery advances benefiting micromolding?
Runyan: Recent years have witnessed significant advancements in materials and machinery that are poised to revolutionize the field of micromolding. On the material front, the development of novel micromoldable materials has expanded the possibilities for intricate and high-performance micro components. Engineered bioresorbable polymers, for instance, are gaining traction in medical micromolding due to their biocompatibility and ability to degrade over time within the body. This allows for the creation of temporary implants that gradually dissolve as tissues heal. Furthermore, advancements in high-temperature thermoplastics are enabling micromolding to be applied in a variety of sectors, where components need to withstand extreme conditions. These innovative materials not only broaden the scope of micromolding applications but also challenge manufacturers to optimize their processes to accommodate new material characteristics and processing requirements.
In parallel, machinery advances are driving greater precision, efficiency, and scalability in micromolding. Micromolding machines with enhanced automation and robotics capabilities are reducing the risk of human error and increasing production throughput. Intelligent real-time monitoring and data analytics systems are being integrated into micromolding equipment, providing insights into process variables and enabling predictive maintenance. Additionally, the development of microinjection units and tooling technologies is facilitating the molding of even smaller and more intricate features. As micromolding continues to push the boundaries of miniaturization, advancements in machinery play a pivotal role in achieving higher quality, tighter tolerances, and greater repeatability. Looking forward, we believe these material and machinery innovations hold the promise of unlocking new frontiers in micromolding, enabling industries to create increasingly complex and functional microcomponents that were once thought to be beyond reach.
What challenges remain in micromolding? What is needed to address them?
Runyan: Micromolding still faces challenges despite its advancements, primarily centered around intricate design complexities, material behavior, and process repeatability. Designing microscale features that can be consistently replicated presents difficulties due to factors like part ejection, undercuts, and maintaining structural integrity. Moreover, the behavior of materials at such small scales can lead to variations in material flow, cooling rates, and part shrinkage, impacting dimensional accuracy and quality. Addressing these challenges necessitates a holistic approach involving close collaboration between design engineers, material scientists, and micromolders. Advancements in simulation software for predicting micromolding outcomes, combined with rigorous material testing and specialized tooling technologies, will be crucial in refining processes, enhancing material selections, and ensuring consistent production of high-quality micro components.
Another challenge is educating a customer/prospect on what is possible regarding thin-wall molding, insert/lead frame molding, and the lack of formal design rules when designing a critical microcomponent. Projects are bespoke to specific customers, so each one will have their own challenges to overcome. At the front end of projects, it is critical to partner with the right strategic micromolder who has the expertise, talent, and bandwidth to ensure that customer project goals are achieved. Picking the right strategic partner for micromolding is just as important as the OEM’s criteria for quality, lead times, and cost targets for projects.
What will Accumold be highlighting at the upcoming BIOMEDevice Boston and MD&M Minneapolis shows?
Runyan: Accumold will be showcasing several new capabilities at both upcoming trade shows. Accumold has been working closely with several customers in the drug-delivery market on a new “all-plastic molded cannula.” The Accumold designed sample is 9 mm long (0.0354 in.) and has a 0.01-mm wall thickness (0.004 in.). This technology can be customized to meet project specifics lengths, material choices, and wall thicknesses. Another capability is micro silicone overmolding and micro silicone part production. We are excited to talk about these and all our capabilities with attendees at both events.
About the Author(s)
You May Also Like